The organic fertilizer manufacturing process for crop straw and animal manure usually consists of pre-treatment, main fermentation, post-fermentation, post-treatment, compounding and other processes.
1. Pre-treatment
The main task is to remove non-fermented foreign matters such as sludge, metals, batteries, etc. in plant residues, crush plant residues, and adjust moisture and C / N value. Reasons for removing non-fermentation foreign bodies: reducing the volume of the fermentation chamber; removing the materials that affect the fermentation, such as metals and batteries, and reducing the chance of heavy metal pollution; removing the hard-to-crush materials such as plastic ropes, which is conducive to subsequent crushing and stirring Reasons for crushing to adjust the size of plant residues: usually crushing makes the moisture of the raw materials uniform to a certain extent, increases the specific surface area of ??the material, increases the area where the material contacts the microorganisms, 2 high 30 solution speed. Theoretically speaking, the finer the material, the better, but in order to ensure a certain gap of the material to ventilate to obtain oxygen, the range of 2 to 30 mm is generally better.
2. Main fermentation
It can be carried out in the open air or in the fermentation device, and oxygen can be supplied to the accumulation layer or the fermentation device by turning the pile or forced ventilation. The first is the decomposition of easily decomposable substances such as sugar and protein, producing CO2 and H20, and at the same time generating heat, which raises the fermentation temperature. In the initial stage of fermentation, the decomposition and fermentation of the substance relies on mesophilic bacteria (30-40 ℃ is the most suitable growth temperature). As the fermentation temperature rises, the high-temperature bacteria with the most suitable temperature of 45-65 ℃ replace the mesophilic bacteria. Various pathogens, insect eggs and weed seeds are killed. Generally, the period from when the temperature rises to when it starts to decrease is called the main fermentation stage, which is 3 to 10 days.
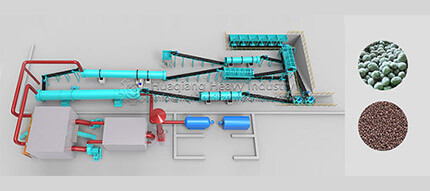
3. Post-processing
In the material after two fermentations, almost all of the organic matter has become finely crushed and deformed, and the amount has been reduced. Once again, a sorting process is performed to remove debris such as plastic, glass, ceramics, metal, small stones, etc. broken.
4. Deodorize
Some fermented products have an odor after the fermentation is finished, and deodorization treatment is necessary. Methods include chemical deodorant deodorization, alkali water and aqueous solution filtration, activated carbon, zeolite, special soil, etc. as adsorbent filtration.
5. Compound
According to the product formula requirements and the nutrient content of the material after fermentation, urea, phosphate fertilizer, and potassium fertilizer are added to the fermentation material to produce an organic-inorganic compound fertilizer, or microorganisms with specific functions are added to produce a biological organic fertilizer.
6. Inspection, packaging, storage
Test and analyze whether the nutrient content, maturity, moisture content, heavy metal content, pathogen content, organic matter content and other indicators meet the product requirements. Weighing, packaging and storage after meeting the requirements.